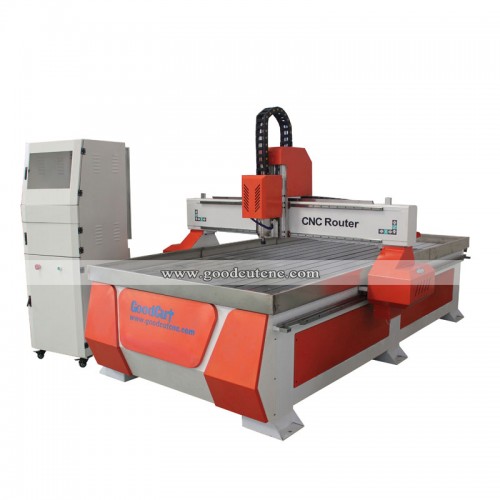
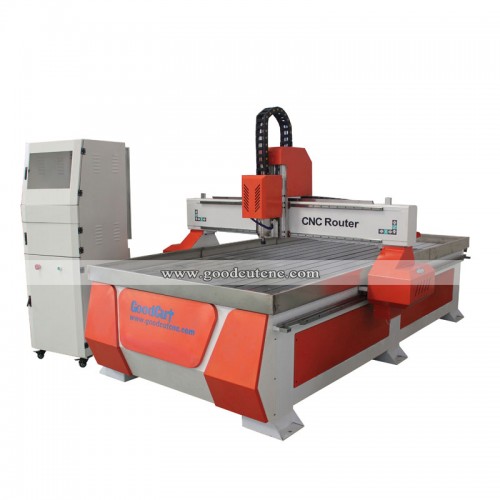
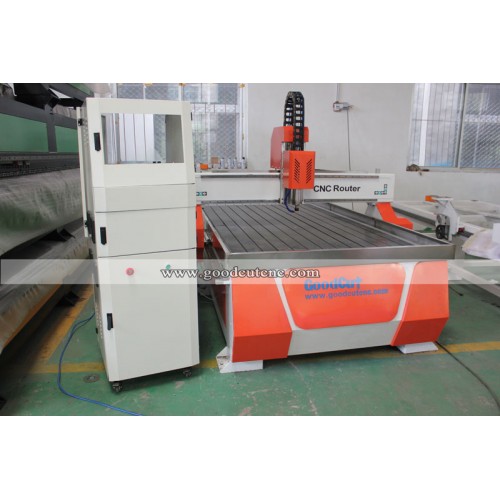
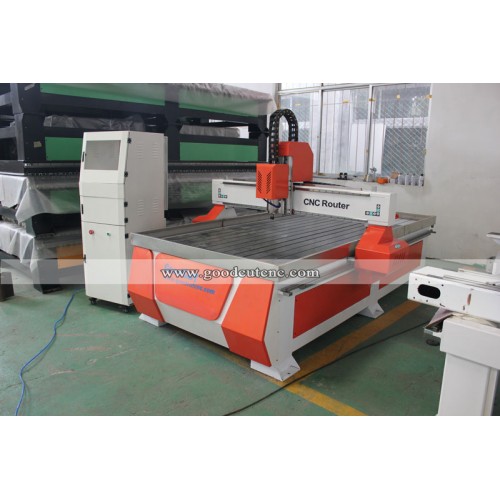
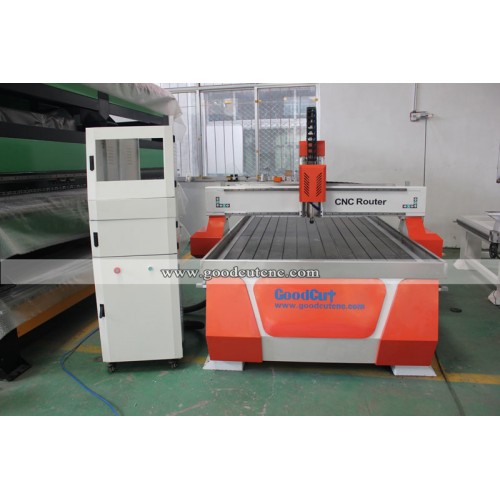
GC-1325W CNC Router with Water Tank for Wood Aluminum Artificial Marble Sand Plastic Sheeting PVC Pipe Cutting Milling Carving
Parameters | |
Model | GC-1325W |
Driver and Inverter | leadshine driver and fuling inverter |
X Y Z Traveling Area | 1300mm*2500mm*200mm |
Table Structure | Aluminum T-Slot |
Spindle Power | 3.2KW Water Cooling |
Cooling system | Spray water cooling system |
Water tank | Yes |
Ball screw | Taiwan TBI |
Max. Spindle Speed | 24000r/min |
Max. Traveling Speed | 12000mm/min |
Max. Working Speed | 8000mm/min |
Processing Accuracy | ±0.025mm |
Reposition Accuracy | ≤0.025mm |
Driving System | Stepper Motor or Servo Motor |
Operation System | NC-STUDIO (optional DSP/Mach 3) |
Software | Type3, Artcam, Ucancam |
Working Voltage | AC 220/380V |
Net Weight/Gross Weight | 1250 KG/ 1400KG |
Feature:
1. High accuracy ball bearing guide screw of taiwan,minimize the slit.
2. Imported linear rail,self lubricating glide.
3. Our routers have the features of recarving after stop and the power failure may be restored.
4. Unique preservation way of the zero point.
5. Use for long time and no distortion.
6. This type is also suitable for advertisement.
7. Iron cast wholly frame, double- screw auto eliminating ball screw, floor-type linear guide transmission.
8. High power water cooling brushless motor
9. Stepper motor could enhance work efficiency.
10. Break-point memory pointesfor 10 pcs, reducing material waste.
11.High compatibility, applicable for CNC software: type3, Artcam, Castmate, Pore, Weitai, variable CAD/CAM etc. It is easily to process relief sculpture, shadow carving, three dimension characters in fancy style etc.
Application:
1. Wood Furniture Industry: Wave Plate, fine pattern, antique furniture, wooden door, screen, craft sash, composite gates, cupboard doors, interior doors, sofa legs, headboards, soft metal and so on.
2. Advertising Industry: Advertising identification, sigh making, Acrylic engraving and cutting, crystal word making, blaster molding, and other advertising materials derivatives making.
3. Die Industry: A sculpture of copper, aluminum, iron and other metal molds, as well as artificial marble, sand, plastic sheeting, PVC pipe, wooden planks and other non-metallic mold.
How To Use A CNC Wood Router?
Step 1. Turn On Machine. Before starting up, ensure that all connections between the computer-controlled wood cutting machine and the computer are normal, and then turn on the power supply of the machine and the computer to enter the system.
Step 2. Mechanical Reset. After starting the system (the system will judge whether the kit has "returned to the machine origin" before entering the active machining), the "return to machine origin" prompt dialog box will appear first, click the corresponding button, and the computer-controlled wood carving machine will automatically return to the wood carving machine origin. And proofread the coordinate system.
Step 3. Check I/O Status. Check the input and output status of each signal, check whether there is a fault signal, to ensure that the machine can process safely.
Step 4. Load File. Before machining, the user usually needs to load the required file, otherwise all the functions of the active machining are invalid. Select [File (F)] -> [Open and Load (O)...] menu, a Windows standard file operation dialog box will pop up, and you can select the file to be cut. Perhaps click the right mouse button in the active machining window to pop up a shortcut menu, select [Open and Load (O)...], and select the desired processing file in the pop-up file operation dialog box. Then after clicking the "Open" button, the processing program is loaded into the system. At this moment, you can click on the "Active" window to check the current file.
Step 5. Manual Operation.
• Display manual operation interface. Click the [Manual] window with the mouse, a manual operation interface will appear, on this interface, you can manually operate the CNC machine for woodworking.
• Manually move. Manual movement can be completed by clicking the corresponding button on the manual operation interface with the mouse. You can also manually move the wood machine through the small number keys on the keyboard. Note that you must first switch the input focus to the manual window. The detailed method is to switch to the manual window first, then click any position of the manual window with the left mouse button, and press the corresponding number key on the keyboard to complete the manual movement.
Step 6. Set Origin of Project. The origin of X, Y, Z, A coordinates in the programming is the project origin. Before machining, first manually move the wood machine's X, Y, Z, and A axis to the orientation of the project origin desired by the user, and clear the coordinate value of the current orientation in the coordinate window (or select [Operation (O )]->[Set the current point as the origin of the project]), so that the current orientation is used as the origin of the project for machining when the programming is executed.
Care & Maintenance
In order to keep all parts of the machine in good condition, it is important to insist on regular maintenance. This can eliminate many potential failures in the bud and prevent vicious accidents from happening. Operators should form a good habit of frequently maintaining the equipment used.
• Before turning on the machine every day, check whether the communication line, motor line, and optocoupler line are loose, and whether the voltage is stable. Then turn on the power of the machine, operate the machine to move back and forth twice, and start working.
• The water-cooled spindle machine tool should ensure the cleanness of the cooling water and the normal operation of the water pump. The water-cooled spindle motor must not be short of water. The cooling water should be replaced regularly to prevent the water temperature from being too high. The circulating water should be as much as possible, and a large capacity can be replaced water tank.
• Regularly clean the heat dissipation and ventilation system of the circuit box. Please regularly check whether the fans on the electric control box are working normally. Regularly clean the dust in the electric control box with a vacuum cleaner and check whether the terminal screws are loose to ensure the safety and reliability of the circuit. use.
• Clean the dust and debris on the exposed guide rail (polished rod), and clean it with No. 2 engine oil. After cleaning, add butter or No. 2 lithium-based grease.
• Clean the sensor (optocoupler, proximity switch) to prevent dust, powder and oil from sticking to the sensor, affecting its sensitivity or causing false touch.
• Move the machine head to the lower left or lower right position to stop to prevent collision, and then cut off the power supply; do not unplug the plug while it is live.
• Maintenance when it is not in use for a long time: When the machine tool is not in use for a long time, it should be powered on 1-2 times a week, especially in the rainy season when the ambient humidity is high, and the machine tool should be run empty for about an hour. Use the heat of electrical components to dissipate the moisture in the numerical control system to ensure stable and reliable performance of electronic devices.
• Maintenance of the inverter: The inverter has been debugged before leaving the factory. It is forbidden to debug and change the line without permission to prevent damage to the motor or the inverter due to data input errors.
• After one day's work is completed, take off the router bit first, and let the spindle chuck and lock nut be in a loose state. Doing so will help extend the life of the spindle chuck. Then we start to clean the work surface, which can be cleaned with a brush; note that it is best not to accumulate debris on the work surface to avoid deformation of the platform.
• The door of the electric control box should be opened as little as possible, and it is forbidden to open the door to work. Generally, there will be dust, wood chips or metal powder in the air during working. Once they fall on the circuit board or electronic devices in the electric control box, it is easy to cause damage. The insulation resistance between devices decreases, and even damages components and circuit boards.
• Regularly check whether the screws of each part of the machine are loose.
• Vacuum pump maintenance tips:
The wire mesh in the suction port of the water circulation air pump is used to prevent foreign dust particles from entering the pump body. The filter mesh should be kept clean at all times to avoid clogging and reduce the pumping speed of the pump. When the water pump is not in use, it should be powered on for a few minutes every few days to prevent the pump body from rusting and cannot operate normally. Loosen the butterfly nut of the vacuum pump, take out the paper filter element and clean the filter screen regularly with high-pressure air. If the filter element is found to be not ventilated smoothly or damaged, it should be replaced in time. According to the length of use, a high-pressure oil gun can be used to oil the bearings of each part.
• Operate in strict accordance with the instructions for use and abide by safe use regulations.
Troubleshooting
1. The motor makes abnormal noise.
Check the motor for overload; the motor may have an internal fault. At this time, it should be repaired or replaced in time.
2. The motor is in the opposite direction.
Directly check whether the motor line is out of phase or change the output UVW terminal (that is, the connection line between the inverter and the spindle motor).
3. The spindle motor heats up.
First check whether the water pump is working, and then check whether the circulating water is lower than the liquid level.
4. The motor is weak or unable to rotate.
Check the circuit, check whether the motor line is out of phase, and whether the cable is short-circuited.
5. The spindle is reversed.
During the working process of the machine, the main shaft reverses due to the connection between the frequency converter and the main shaft, and it only needs to replace the connecting line.
When the spindle is reversed, if the MDF is cut, the cutter will break, and the cutter may break when it is installed and used.
Even if it doesn't break, it will be burned red. Therefore, when this abnormal phenomenon occurs, the operator should immediately stop the machine and check the main shaft.
6. During the working process, there is a phenomenon that the cutting is dislocated and the direction is opposite. After starting up, if there are irregular movements when clicking continuously and quickly, it is a "phase loss" fault. Check the circuit between the output terminal of the driver and the stepper motor, find out the open circuit, and reconnect the fault to solve it.
7. When the machining axis is controlled manually or automatically, the machine tool does not respond:
• Check whether the data cable is connected firmly, if it is loose, connect it correctly.
• Check whether the drive circuit interface is loose or disconnected, and reconnect.
• Check whether the host power circuit is powered off.